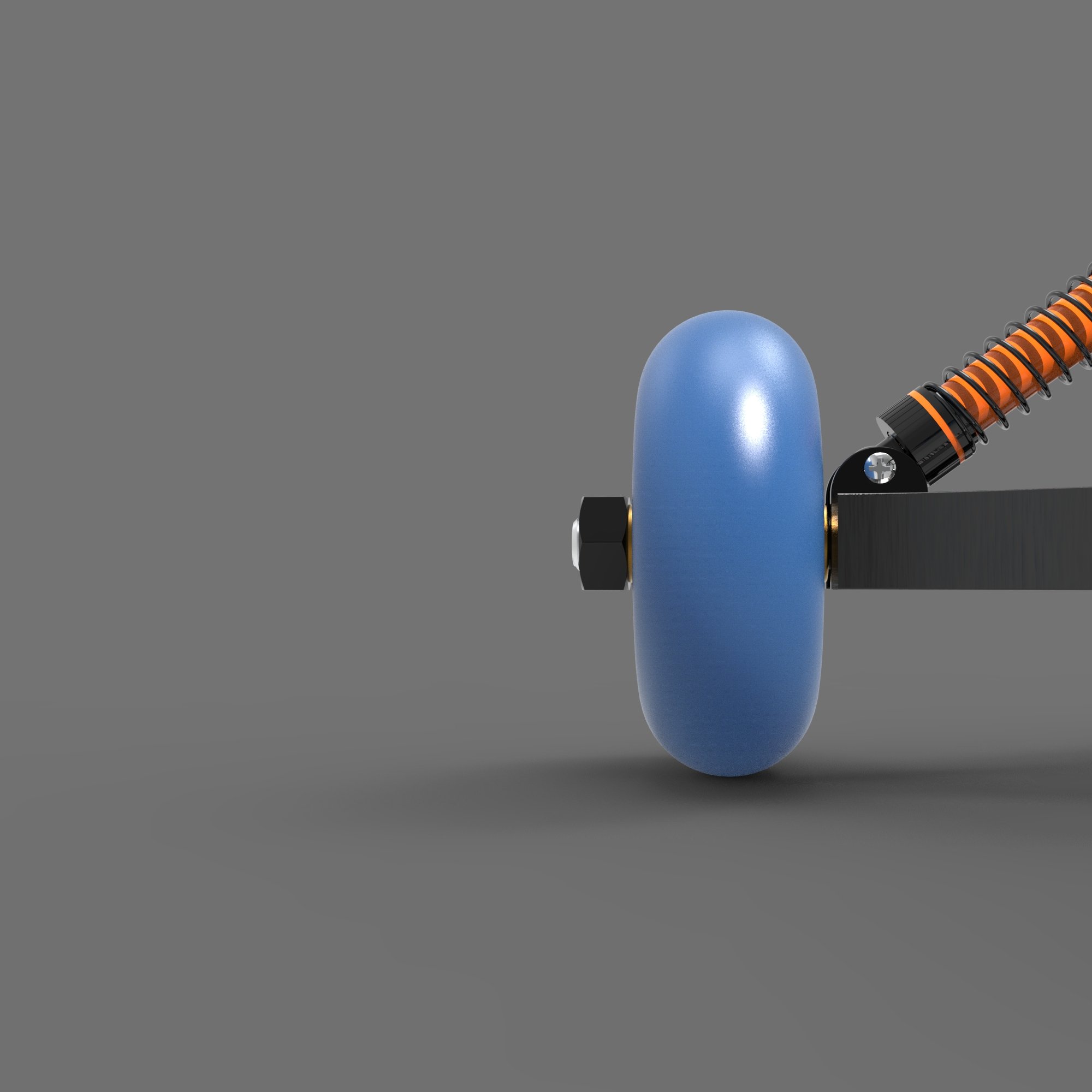
Metal Motion Vehicle
Design and manufacture a three-wheeled vehicle.
The vehicle will be manufactured from steel rod, sheet metal, and three inline skate wheels (~ 3"). The vehicle must be capable of covering a distance of 35’ down a ramp, relying solely on gravity for propulsion.
The vehicle will be evaluated on the following issues:
Distance: The vehicles will start at the top of the Creative Arts building ramp and travel as far as possible into the common area.
Speed: The traveling speed will be evaluated (35) feet in (4) second
Control: Design and manufacturer the vehicle to travel in the straightest possible line down the ramp.
Materials:
¼ inch steel rod 10’ long
16"x6" sheet metal 20-22 gauge
Rivets, bolts & nuts, washers, paints, wax, bondo filler
Three Inline polymer Wheels and bearings
Project Timeline
Phase 1: Research and Analysis
April 4st
Understand Testing Environment
Research examples of past projects
Phase 2: Ideation
April 11th
5-10 Concept Sketches
Seek Feedback and design direction from Professor
Phase 3: Prototype
April 18th
Create Foam Core Mockup
Design 3D Cad model
Final design Approval from Professor
Phase 4: Fabrication and Testing
April 25th
Compile Materials
Identify tools needed for fabrication
Conduct trial runs and make adjustments where necessary
Phase 5: Results and Deliverables
May 2nd
Competion Results
Final Presentation
Findings and Takeways
-
After understanding the purpose/goals of the project, scope, timeline, and availabile resources; the next phase is to conduct research.
Analyze the conditions and influences affecting the use of gravity force in the design.
Considerations: Distance, Control, Speed, gaps between concrete slabs, debris, alignment angles, where to apply load, low profile chassis, extended wheelbase, and application of suspension.
Test Environment: Fine Arts Building Ramp
Ramp angle: ≈30°, Ramp length: ≈60’
Shifting your weight to the back of the car before starting, gives you more potential energy. This extra energy, when converted to kinetic energy, makes the car go faster down the ramp. Both cars start at the same speed, but the one with weight at the back gets a boost and accelerates for a longer distance on the flat part of the track.
Distance and Speed: (Dragster)
The length helps keep the car stable under high speeds.
-
It all begins with an idea.
Conceptual Design: Develop 5-10 design concepts considering the materials and criteria specified.
Design Considerations: Aerodynamics, testing environment, gaps between concrete slabs, chassis design.
-
foam core mockup, 3D model
Challenges: Corrupt CAD files
→
↓
↓
Fabrication
-
Fabrication Challenges:
- Weak welding
- Learning on the Fly (No prior knowledge of welding)
- Fitment and Material Challenges
- Safety (Grinding metal, situational awareness for others
-
After fabrication was completed, multiple runs were conducted and alignments angles were adjusted accordingly to ensure straightest possible descent.
-
Farthest vehicle travelled with distances of 140’ +
weight: ≈ 4lbs
Speed: 0-35’ in 3.1 seconds
Learning Outcomes:
Save files often and make copies
Mig Welding, Creating Jigs
weight distribution
How to create technical Drawings/ List of Materials